During a recent visit to the Guntamatic factory in Puerbach, Upper Austria, we were given a guided tour of their biomass boiler factory. This was part of our annual visit for the MCS inspection, which Guntamatic passed with flying colours.
Guntamatic manufactures all of its own structural components, which is why parts can be guaranteed to be available for 20 years. With the commercial Renewable Heat Incentive (RHI) running for 20 years, the long term usage and reliability of your Guntamatic biomass boiler can therefore be assured for the duration of the scheme. Any issue with your boiler will potentially affect or lose you your RHI payments, therefore it is reassuring to know that, with Guntamatic, you are in safe hands.
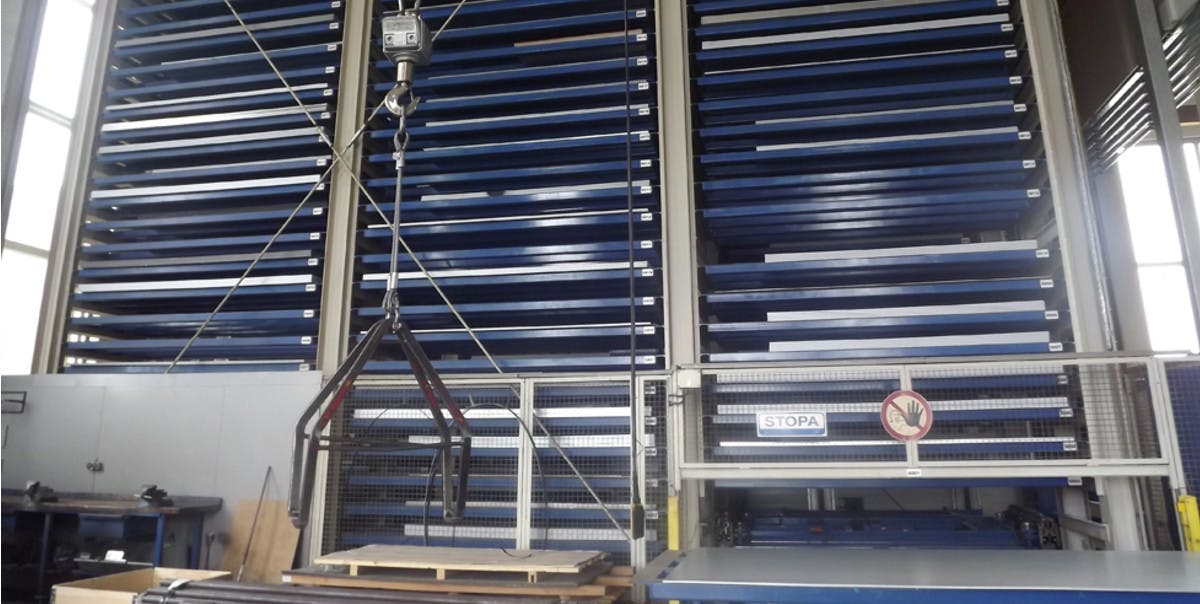
The first stage is for the flat sheets of steel to be cut to shape, ready to move on towards being put together to form the structural frame on which the rest of the biomass boilers will be built. We were very impressed to see the thickest and highest grades and gauges of steel are used to give Guntamatic’s biomass boilers an incredibly strong foundation. There's no disputing the fact that these boilers are built to last.
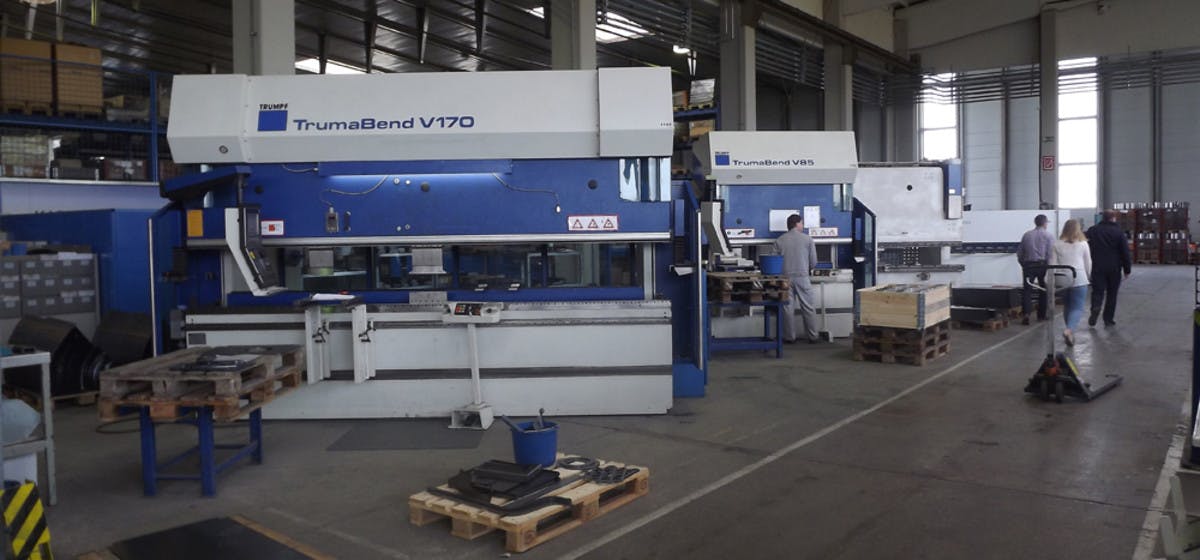
Once cut into shape, the pieces of steel are cut, shaped and formed in the TrumaBend machine in order to fit to the respective biomass boiler and holes drilled which will aid further work along the production line.
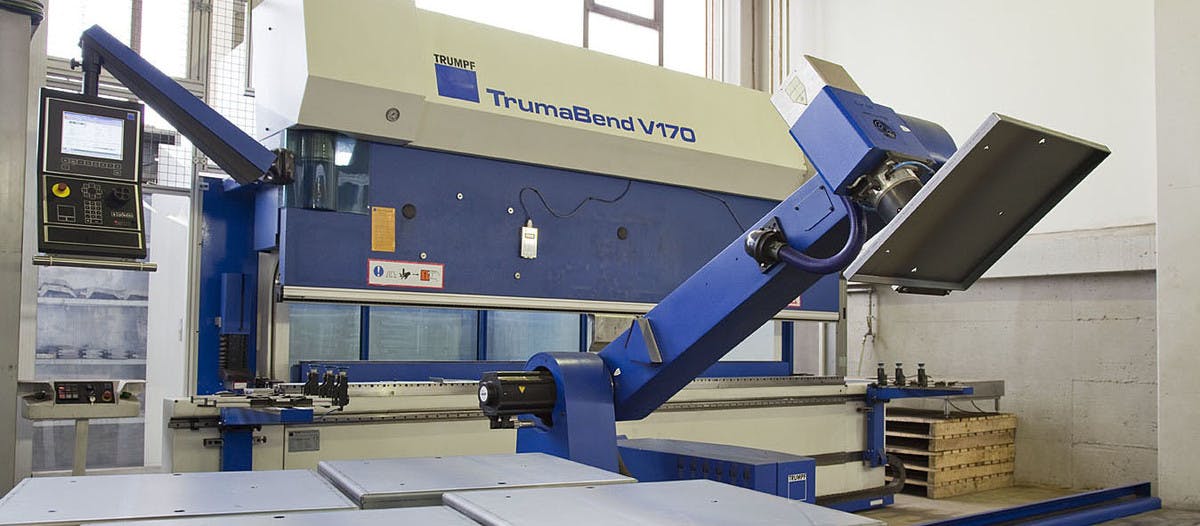
Robots move the pieces of formed steel along the production line to the next step of their journey towards becoming a biomass boiler.
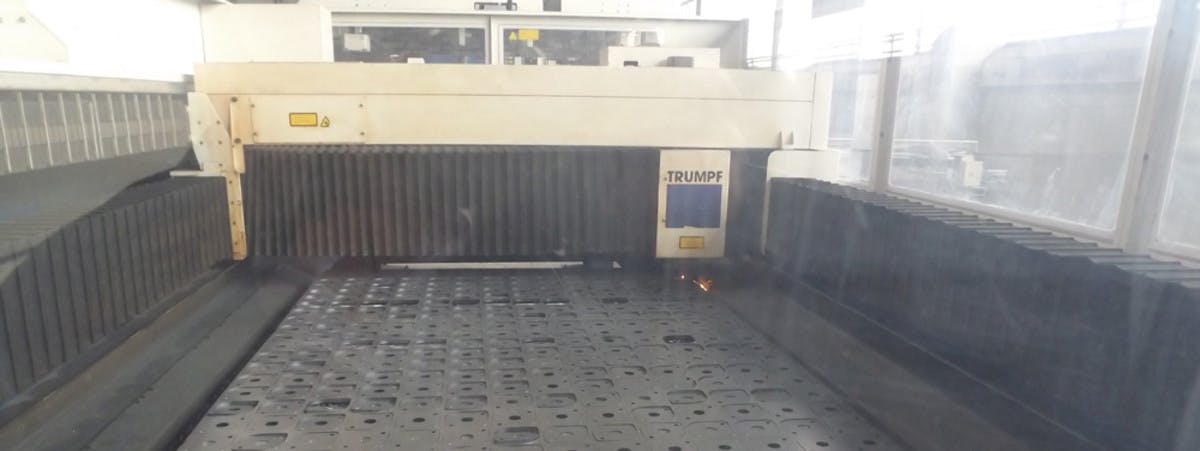
Further along the production line, the pieces of steel are welded together in order to form the structural shape of the BMK, Biostar, Biocom, Powerchip, Powercorn or PRO ranges of biomass boilers.
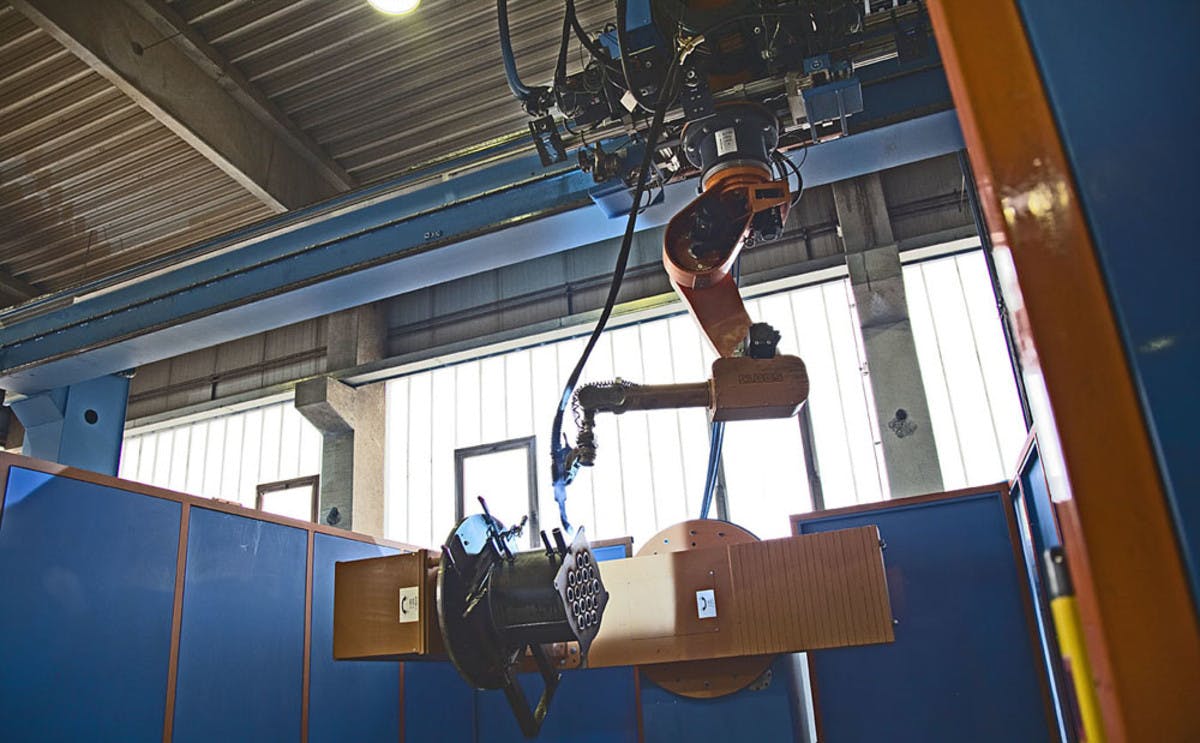
The pieces then start to take shape. The image above shows the housing that will contain the turbulators inside the biomass boilers.
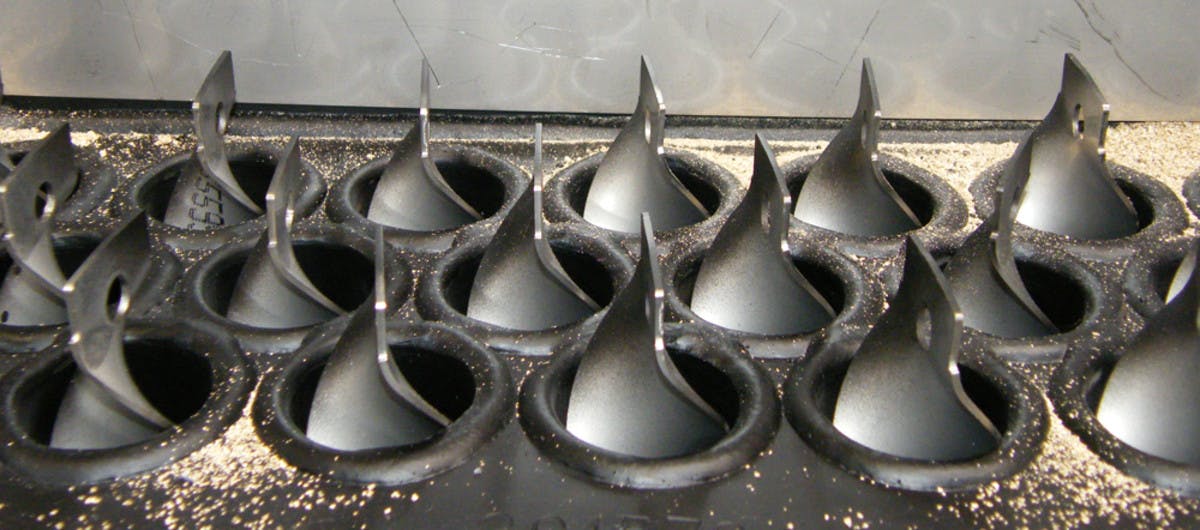
These will eventually be sealed to ensure the unit will keep the heat exchanger clean from efficiency-reducing deposits, giving you up to 96% heating efficiencies and ensuring you gain the most heat for your money.
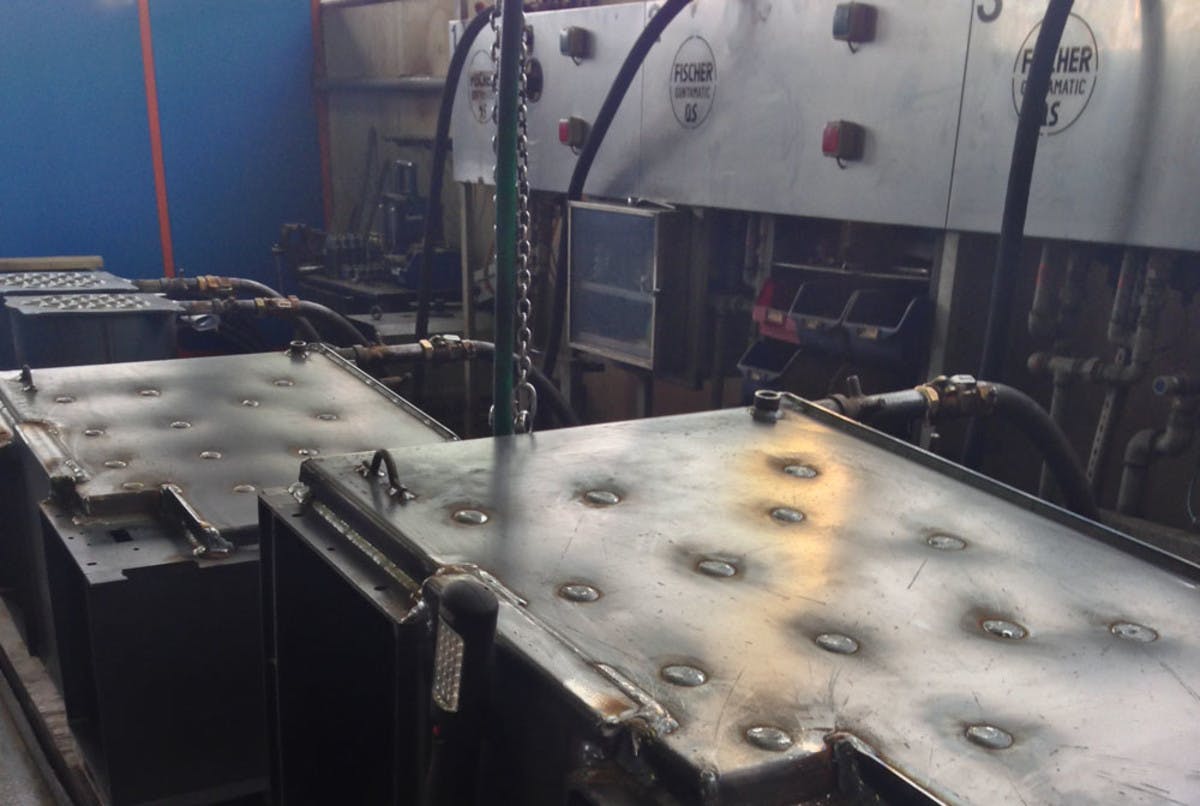
At this stage in the process, it is evident that Guntamatic’s decision at an early stage to automate its own site as opposed to using cheap production abroad has paid off. Every single detail and aspect of the production has subsequently been refined over 50 years, whilst output capacity has continued to dramatically increase.
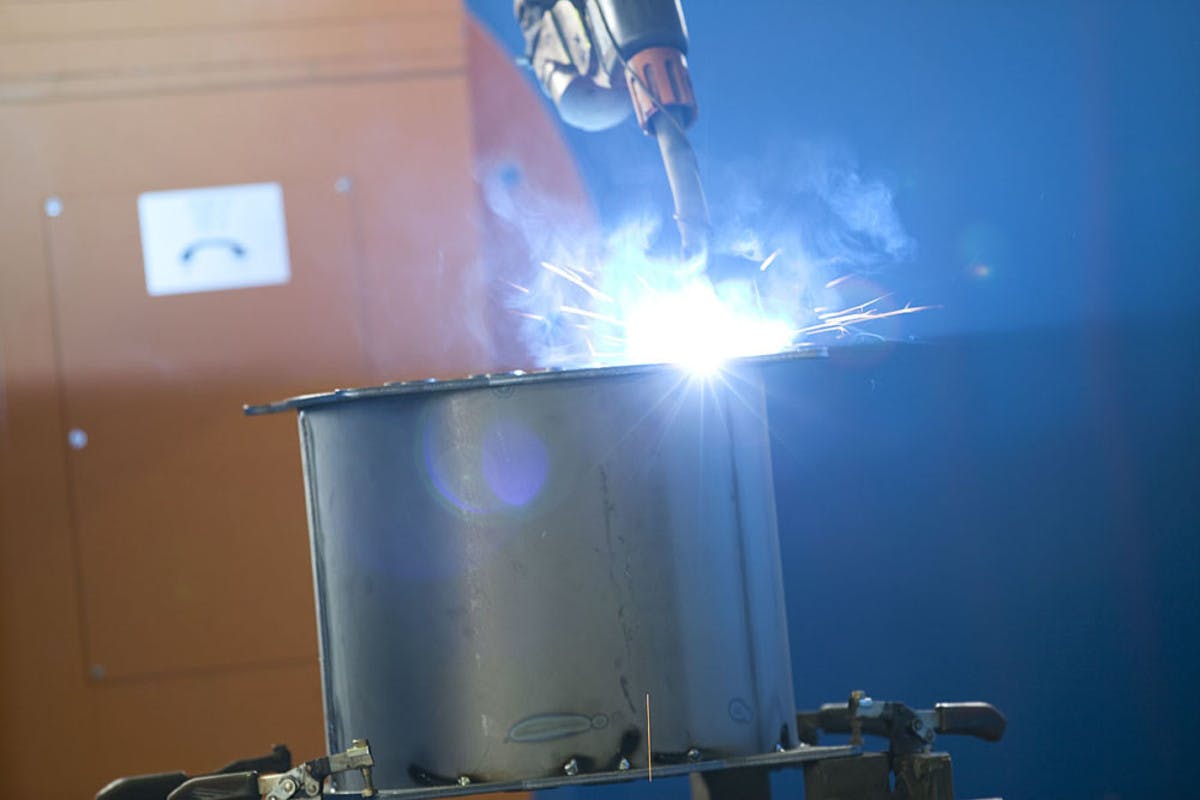
This has enabled the company to keep a tight control on quality whilst perfectly balancing new generation know-how with significant investment in innovation, systems and quality control.
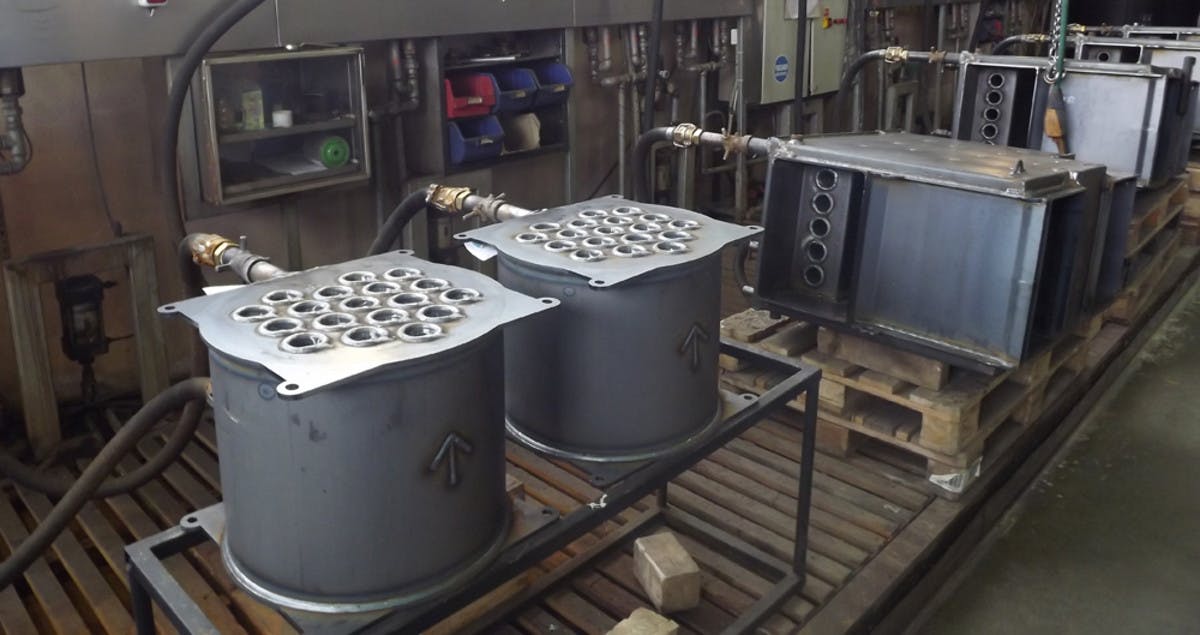
Once the internal structures are complete, they move further through the factory, where they are made ready for the rest of the internal electrical components.
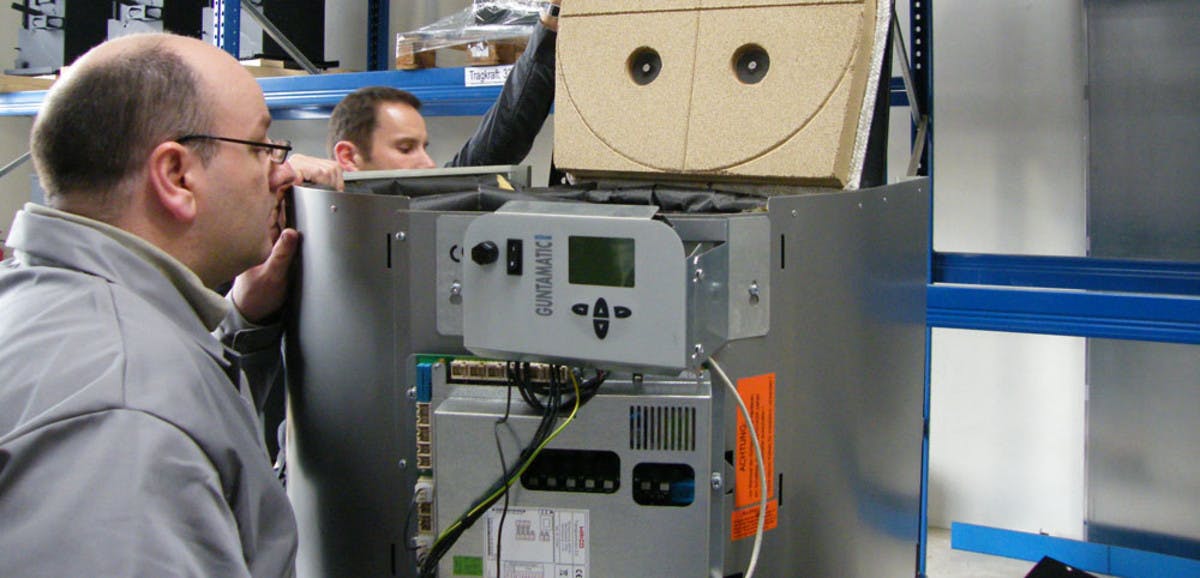
Al this point, the internal structures of the biomass boiler ranges have been completed and are now ready for the internal workings and casings to be added.
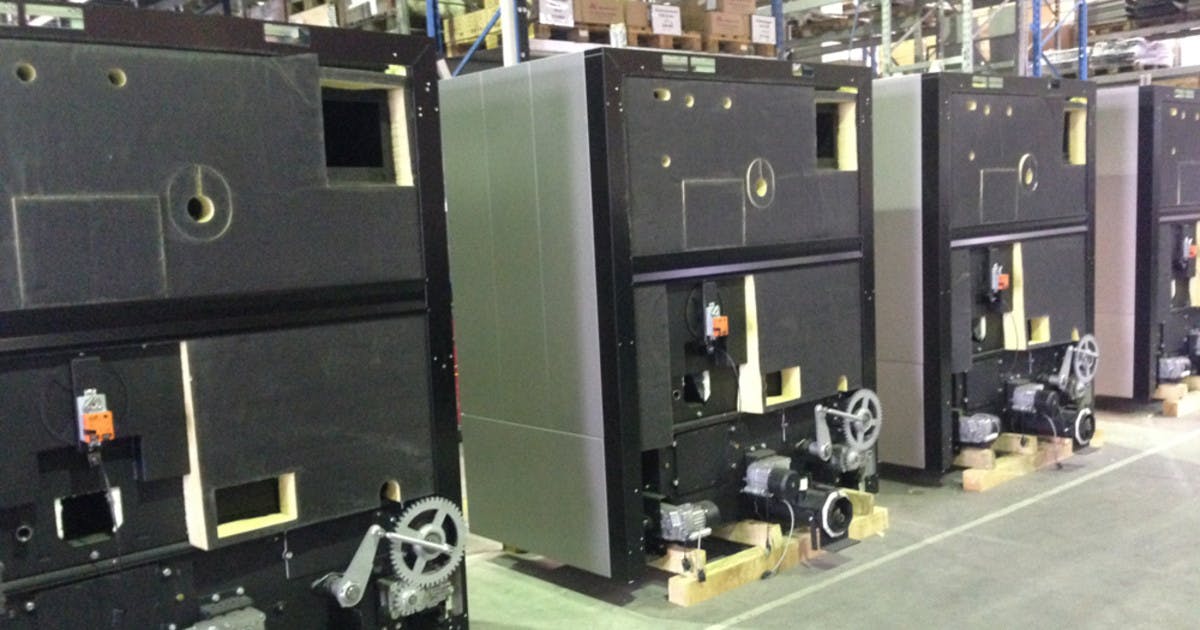
Once the casings and electrical components have been applied, the biomass boilers start to look more like the finished product. In this case, you can see the Guntamatic Powerchip, a multi-fuel biomass boiler that is able to run on wood chips, wood pellets, grain or miscanthus.

At this work station, the 200 litre fuel hoppers for the Biostar wood pellet boilers are made ready to be attached to the boilers.
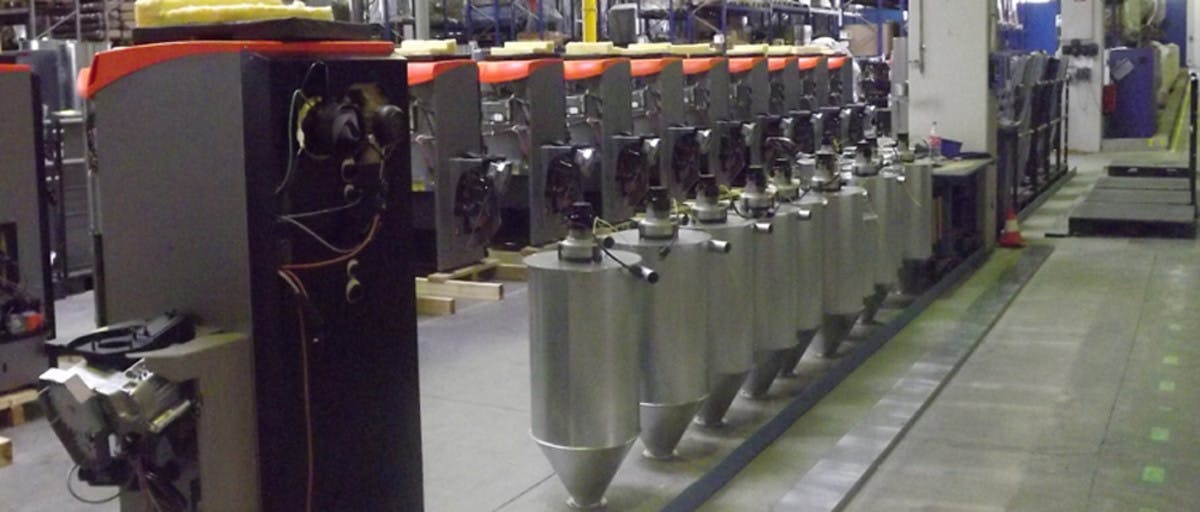
This series-production approach has been refined over the years, with each stage broken down into specialist tasks, completed by highly trained and experienced experts. Here you can see the recently launched PRO, with heat outputs from 175-1,000kW, which makes them ideal for larger commercial and industrial applications.
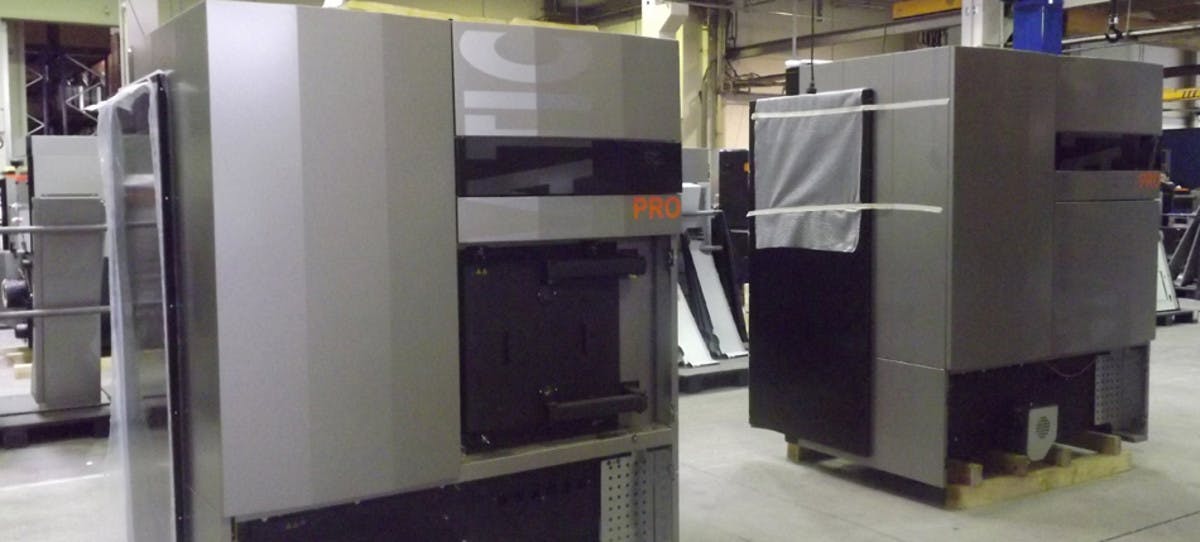
The wood pellet and wood chip biomass boiler, PRO, has been well received in the UK, with several installations already successfully completed by Treco. Below is an image of a PRO, along with its agitator, packaged and ready to be shipped to the UK.
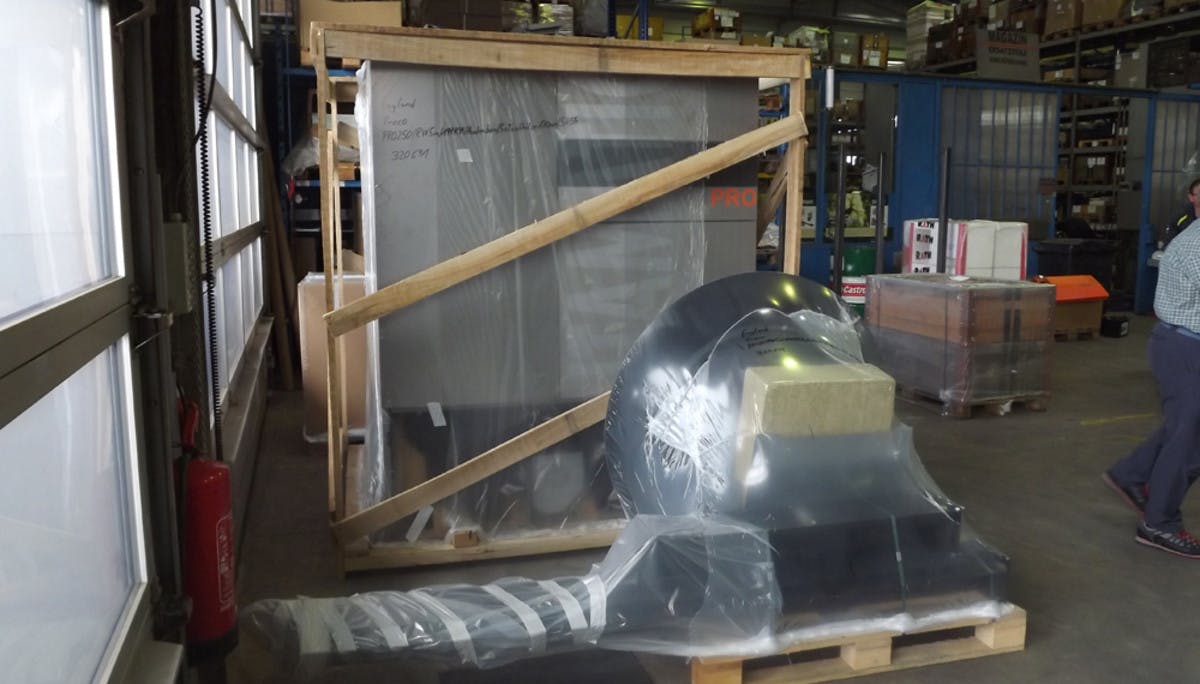
With a busy winter months predicted, Guntamatic begins to build up stocks during the quieter summer period in order to meet the growing international demand for their range of highly efficient and low-emission biomass boilers.
We were also fortunate to be given a tour of the additional warehouse and factory facilities which were recently completed as part of an expansion programme to give Guntamatic a further 10,000m2 of work area, totalling to a significant 25,000m2 of floor space. We have never seen so many biomass boilers in one space before! Seeing all of them together really brings home just how many systems they sell in a year and how Guntamatic are truly a market-leading international player.
Having never seen the production line first hand, it was fascinating to see how Guntamatic brings a biomass boiler to life. Until you actually see the extent of Guntamatic's factory and production facility, it is hard to fully appreciate just how much thought and planning has gone into the whole process during the past 50 years.
It is easy to see, with these photos giving you a sneak guided tour, why Guntamatic’s biomass boilers has been finessed to become the best on quality on the market today.
We'd like to thank the export manager, Walter Wagner, for accommodating us and giving us the opportunity to see this all first-hand.
Find out more about Treco
Careers at Treco
If you’re interested in working for Treco start here for more information about what it's like to work for us and the latest on career opportunities.
Our work
Read a selection of the various projects we've worked on and just some of the examples of our work. With over 700 installations nationwide, you'll be sure to find one in your sector and geographically close to you.