Hollyfield Poultry Farm
Biomass boiler solution heats farmhouse and 5 poultry houses, improves bird welfare and saves ongoing costs
Key Facts
Location
Tiverton, Devon
Project included
- 3 x Guntamatic 100kW Powerchip boiler systems, flue & thermal store
- All aspects of district heating scheme
Client managed
- Trenching and laying underground insulated pipe and services
- Building high-specification, custom built boiler houses and fuel stores
Fuel consumption
Approximately 120 tonnes of wood chips per annum
Fuel cost saving
50- 80% per kWh (Source: Biomass Energy Centre)
CO₂ saving
Approximately 90 tonnes per annum ( chip vs LPG)
RHI payments
A project of this size would gain upwards of £33,000 every year for 20 years, index linked to inflation
ROI
5-6 years (RHI income & fuel cost saving)
Downloads
The biomass boilers have given us a much improved environment for our birds. We now have total control of humidity levels, and the dry heat has increased bird welfare and reduced the cost of inputs. The significant investment also provides a long term financial return to the farm
Overview
Hollyfield is a poultry farm near Tiverton in Devon which rears 31,000 free-range birds per cycle in five purpose built sheds.
The challenge
Bird welfare is a high priority on the farm. Management of the poultry houses’ environment is key to this. Direct LPG heaters were previously being used which were an inefficient, expensive source of heat. They were detrimental to the poultry house environment and led to increased humidity, CO₂ and ammonia levels.
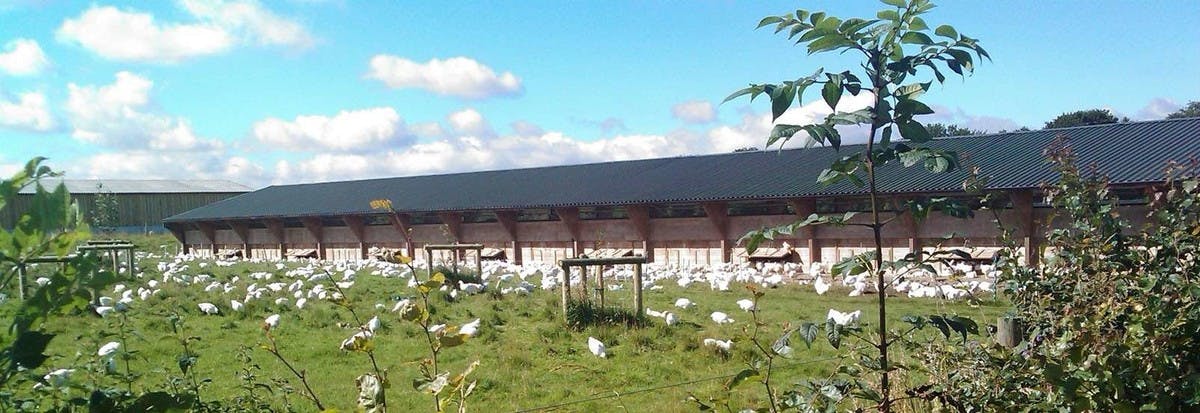
As a result, a large amount of ventilation was needed, leading to more heating expense to maintain temperature. This, combined with regular top-ups of bedding was costing the farm a lot of money.
Our custom solution
The solution was indirect heating from water-air heat exchangers, powered by a renewable fuel source. An efficient 'dry heat' now ensures optimum litter and air quality throughout the crop cycle for improved bird welfare and performance, along with reduced input costs.
Treco installed and commissioned three biomass boilers into boiler houses custom built by the client. The solution included;
- 3 x top of the range 100kW Guntamatic Powerchip biomass boilers (with fully automated wood chip fuel delivery systems).
- 5m agitator for each boiler allowing 60m3 of fuel storage and ensuring less than four fills a year.
- A 2,000 litre thermal store, per boiler.
- High efficiency, low energy modulating main system pumps.
- 190m of twin underground pre insulated pipe.
- Class 2 RHI eligible ultrasonic heat meters complete with certification.
- 10 x heat exchanger assemblies and pipework.
- Total project management and submission of RHI application.
- 5 x environmental control systems (including humidity control).
- Commissioning, programming and end user training.
- 3 x single to three phase adaptors.
More details on this specific biomass boiler used on this installation can be found on the Guntamatic Powerchip page, with further details of our entire range available through the biomass boilers page.
The incentive
A project of this size would gain upwards of £33,000 every year for 20 years, index linked to inflation.